Compressors are machines that increase the pressure of gas or air for various applications. Each compressor type differs in its design, operation, and efficiency.
Compressors play a crucial role in various industries such as manufacturing, construction, automotive, and aerospace. These machines are designed to increase the pressure of gas or air, making them essential for powering various tools and equipment. Compressors come in different types, including rotary, reciprocating, and centrifugal, each with a unique design and function.
Reciprocating compressors use pistons to compress air, while rotary compressors use impellers or rotors to create pressure. On the other hand, centrifugal compressors rely on centrifugal forces to increase the pressure of the gas or air. Understanding the differences between these compressors is essential in selecting the right machine for your specific application.
What Is A Compressor?
Compressors are mechanical devices that increase the pressure of a gas or air to provide power to various industrial applications. These machines are available in different types, such as reciprocating, screw, rotary vane, and centrifugal, each having its unique application areas and benefits.
An Overview Of Compressors
A compressor is a mechanical device that is designed to increase the pressure of a gas or air by decreasing its volume. In simple terms, a compressor can be thought of as a pump that compresses the air or gas to increase its pressure. Compressors are used in a variety of applications, including HVAC systems, refrigeration, and industrial processes.
Importance Of Compressors
Compressors play a critical role in many industries, particularly in the manufacturing and processing sectors. Compressed air is used to power machinery, convey material, provide pressure, and perform other important functions. Compressed air is also used to clean machinery, products and to operate power tools.
It is imperative to choose the correct compressor design for your specific requirement. Reciprocating, rotary screw, and centrifugal compressors are the most common types of compressors available on the market, and each has its own unique advantages and disadvantages.
Reciprocating Compressors
Reciprocating compressors are positive displacement compressors that use pistons to compress the gas or air. They are efficient and can deliver high-pressure output. They are usually found in smaller applications like refrigeration units and air conditioners.
Rotary Screw Compressors
Rotary screw compressors are positive displacement machines that use two helical screws to compress the gas or air. They are energy efficient and have low maintenance costs, making them suitable for industrial applications that require continuous compressed air supply.
Centrifugal Compressors
Centrifugal compressors use high-speed impellers to accelerate and compress the gas or air. They are best suited for high volume applications, but they have a lower efficiency compared to reciprocating or rotary screw compressors.
Understanding the differences between compressor types can help to make the right choice when selecting a compressor for your specific application. In the next post, we’ll discuss the factors you must consider when selecting a compressor to meet your needs.
Types Of Compressors
Compressors come in different types, each with its unique features and purposes. Understanding these types and choosing the right one for your needs is vital in ensuring proper compression and system optimization. Below are some of the most common types of compressors:
Reciprocating Compressor
Reciprocating compressors work by drawing in air, trapping it in a chamber, and then decreasing the chamber’s volume to compress the air. The compressed air is then released, and the process begins again. These compressors are commonly used in small to medium-sized applications, such as air conditioning units, refrigeration systems, and pneumatic tools.
Rotary Compressor
Rotary compressors use rotating vanes or blades to compress air. These compressors are more efficient and quieter than the reciprocating compressor, making them an ideal option for larger systems and industrial applications, such as gas pipelines and pneumatic conveyors.
Scroll Compressor
Scroll compressors operate using two spiral-shaped components that rotate in opposite directions. One component remains stationary, while the other moves, compressing the air as it moves inward. These compressors are commonly used in applications where continuous air supply is required, such as refrigeration and air conditioning systems.
Centrifugal Compressor
Centrifugal compressors use centrifugal force to compress air. Air enters the center of the compressor, where it is flung outward at high speeds, generating pressure. These compressors are suitable for large-scale industrial applications, such as natural gas processing and petroleum refining.
How Do Compressors Work?
If you are a professional in the field of construction, HVAC, or auto repair, you are probably already familiar with compressors. They are essential machines that are used for a variety of tasks, such as powering pneumatic tools, inflating tires, and even refrigerating food in your fridge. But how exactly do compressors work? Let’s explore the basics.
Compressor Basics
A compressor is a device that increases the pressure of a gas or air by reducing its volume. They work by sucking in low-pressure gas or air and then increasing the pressure inside a closed chamber, which is then released through an outlet pipe or valve. This process can be done using various types of compressors, but they all work on the same principle of reducing the volume of air or gas to increase its pressure.
Components Of Compressors And Their Functions
The components of compressors can vary depending on the type of compressor you are using, but some common elements include:
Component | Function |
---|---|
Motor | Drives the compressor’s pump or piston |
Pump | Draws in and compresses air or gas |
Tank | Stores compressed air or gas for later use |
Pressure Switch | Controls the compressor’s operation by turning it off when the maximum pressure is reached |
Regulator | Controls the pressure output of the compressor |
Some compressors may also have additional features such as filters, coolers, and moisture separators to ensure clean and dry air supply for your application.
- Compressors are used for a variety of tasks, including powering pneumatic tools, inflating tires, and refrigerating food.
- They work by sucking in low-pressure gas or air and then increasing the pressure inside a closed chamber.
- Some common components of compressors include a motor, pump, tank, pressure switch, and regulator.
Now that you have a basic understanding of compressors and their components, you can choose the best one to suit your needs.
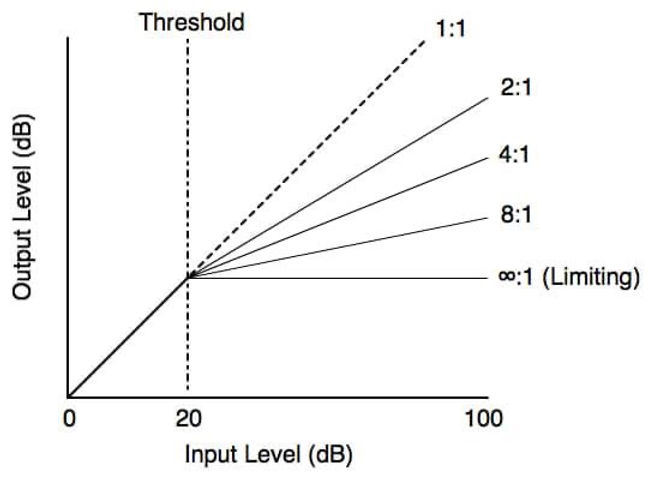
Credit: www.audiomixingmastering.com
Factors To Consider When Selecting A Compressor
Selecting the right compressor can be a daunting task. Several factors need to be considered before making a purchase, such as the type of compressor, the task at hand, and the required output. Understanding the different types and their features can help narrow down the best option for your needs.
When selecting a compressor, it is important to consider a variety of factors such as the applications, air quality requirements, operating cost, and maintenance. Knowing what these factors are and how they apply to your specific situation can help you select the right compressor for your needs.
Applications
The first factor to consider when selecting a compressor is the applications you will be using it for. Compressors are used for a variety of tasks, including powering air tools, spray painting, and operating production machinery. Knowing the specific application requirements will help you choose the right compressor type and size. For example, if you need a compressor for spray painting, you will need to choose a compressor with a low CFM rating that produces clean, dry air.
Air Quality Requirements
Another important factor to consider when selecting a compressor is the air quality requirements for your application. Different applications require different levels of air quality, and compressors can produce varying levels of air purity. For example, if you are using a compressor for medical purposes or in a clean room, you will need a compressor that produces air that is free from oil and other contaminants. In contrast, applications such as powering air tools may not require such high air quality.
Operating Cost
The operating cost of a compressor is another important factor to consider. The cost of operating a compressor can vary greatly depending on the type of compressor, its efficiency, and its maintenance requirements. Choosing an energy-efficient compressor can help to save on operating costs over time. It is also important to consider the cost of maintenance, including regular maintenance and any repairs that may be needed over time.
Maintenance
Finally, maintenance is an important factor to consider when selecting a compressor. Different types of compressors have different maintenance requirements, and it is important to choose a compressor that is easy to maintain and repair. Proper maintenance and regular inspections can help to prolong the life of a compressor and prevent costly breakdowns. In conclusion, selecting the right compressor requires careful consideration of a variety of factors, including the applications it will be used for, air quality requirements, operating cost, and maintenance requirements. By taking the time to understand these factors and how they apply to your specific situation, you can make an informed decision and choose the right compressor for your needs.
Advantages And Disadvantages Of Compressors
Compressors offer an efficient method for generating and storing compressed air or gas, making it easier to transport or utilize in various applications. However, they can also be expensive and require regular maintenance to prevent malfunctions or breakdowns. Understanding the different types of compressors and their advantages and disadvantages is crucial to determining the right one for your specific needs.
Understanding the advantages and disadvantages of compressors is vital before purchasing one. A compressor is a device used to increase the pressure of a fluid or gas. They come in different types, sizes, and capacities, each with its own set of benefits and drawbacks. In this blog post, we will delve into the pros and cons of using compressors.
Pros Of Using Compressors
Compressors have numerous benefits, making them ideal for various applications. Some of the advantages are:
- Enhanced efficiency: Compressors can store gas or air for use on demand, which enhances productivity by allowing continuous operation. They reduce the amount of time spent waiting for pressure to build up.
- Increased power: Compressed air or gas provides a reliable source of power. It can power your tools, equipment, and pneumatic machines, making it a preferred alternative to electricity.
- Cost-effective: Compressed air or gas is cheaper than electricity, making it a more cost-effective solution in the long run.
- Safe: Compressed air or gas is safer than electricity since there is no risk of electrocution or fire. Moreover, it does not produce sparks, making it ideal for hazardous environments.
- Multifunctional: Compressors have multiple uses, from inflating tires to powering industrial tools. Their versatility makes them an excellent addition to any home or business.
Cons Of Using Compressors
Despite the numerous benefits of compressors, they have some drawbacks, which include:
- High maintenance: Compressors require frequent maintenance to ensure they operate optimally. They need regular oil changes, filter replacements, and belt adjustments, among other things.
- Noise: Air compressors produce a loud noise during operation, which can be uncomfortable for some users. This is especially important to consider when using a compressor in enclosed spaces.
- Size and weight: Some compressors can be large and heavy, making them difficult to move from one location to another.
- Environmental impact: Compressed gas can have an adverse impact on the environment if not handled correctly. It can cause air pollution and contribute to global warming.
- Energy-intensive: Compressors require a lot of energy to operate, which means higher energy bills.
In conclusion, understanding the pros and cons of compressors is crucial to determine which one is best suited for your needs. Compressors have several advantages, including enhanced efficiency, increased power, cost-effectiveness, and versatility. However, they also have some drawbacks, such as high maintenance, noise levels, environmental impact, and high energy consumption. By weighing the pros and cons, you can make an informed decision on the type of compressor that is ideal for your specific needs.
Maintenance And Troubleshooting
Understanding compressors is crucial for proper maintenance and troubleshooting. Different types, such as reciprocating and rotary screw compressors, have varying designs and functions. Familiarizing oneself with their differences can help identify issues and prevent breakdowns.
Preventive Maintenance Tips
Regular maintenance of compressors is significant to ensure optimal performance and longevity. Here are some preventive maintenance tips to help you maintain your compressor for optimal operational efficiency:
- Keep the compressor clean and free from debris and dirt buildup. Oil and water filters should be checked regularly as well.
- Check the oil level regularly and change it when necessary. Dirty oil can lead to increased wear and tear and decreased performance.
- Ensure all hoses and fittings are free from cracks, leaks, and other signs of damage.
- Invest in a regular inspection by a professional to ensure all parts are in good working order.
Common Compressor Issues And Solutions
Despite regular maintenance, compressors can still experience issues. Here are some common compressor issues you may encounter and their possible solutions:
Issue | Solution |
---|---|
The compressor fails to start and make any noise. | Check the power supply and circuit breaker. If the issue persists, consider checking the pressure switch or motor. |
The compressor is making loud, unusual noises while running. | Check for loose parts, damaged bearings, or broken components that may require replacement or repair. |
Low or no pressure output from the compressor. | Check the air filter, air intake, and valves. If all seem okay, the compressor’s piston rings or valve plate may be in need of replacement. |
Excessive heat or smell from the compressor. | The issue may be due to overheating caused by low oil levels, dirty oil, or damaged components. Check the oil level and replace if necessary and seek professional maintenance. |
Final Thoughts
Preventive maintenance is crucial in ensuring the proper functioning of your compressor. In case of any issues, it is best to seek professional assistance to prevent further damage. With the right maintenance routine in place, your compressor can last for years while performing optimally.
Frequently Asked Questions Of Understanding Compressors And Their Differences
What Are The 3 Types Of Compressors?
The 3 types of compressors are centrifugal, reciprocating, and rotary screw compressors. Centrifugal compressors use a rotating impeller to compress air, while reciprocating compressors use pistons in a cylinder to compress air. Rotary screw compressors use two interlocking screws to compress air.
What Are The Differences Between Air Compressors?
Air compressors differ in their size, power source, PSI capacity, and lubrication type. Some are portable and suitable for small applications, while others are stationary and designed for industrial use. Choosing the right compressor depends on your application needs, budget, and maintenance requirements.
How Do I Know What Compressor To Use?
To determine the right compressor, consider the purpose, power source, required pressure, airflow, and tank size. Evaluate the tasks the compressor will perform, such as powering airbrushes or operating pneumatic tools. Determine the power source, whether electric or gas. The required pressure, airflow, and tank size depend on the task to be performed.
What Are The 4 Types Of Ac Compressor?
There are 4 types of AC compressors: reciprocating, rotary, scroll, and variable speed. The reciprocating and rotary compressors are the most common, while the scroll and variable speed compressors are more energy efficient but less common.
Conclusion
To wrap it up, compressors are essential for various businesses requiring compressed air or other gas streams. Selecting the right type of compressor should be guided by the application requirements, as different compressors have varying features and limitations. Remember, choosing the wrong compressor can hurt your productivity, and ultimately, your bottom line.
Always consult with an expert for professional advice, and ensure you pick the compressor best suited for your needs.