Compression meters are devices used to measure the compression of an engine’s cylinders during operation. These meters are essential tools for monitoring the health and performance of an engine.
Compression meters are vital for maintaining optimal engine performance and detecting mechanical issues before they become major problems. By measuring the compression levels in an engine’s cylinders, these devices can help identify worn or damaged internal components, such as piston rings or valves.
This information can be used to guide repairs and prevent potential engine failure. Compression meters are commonly used by mechanics, automotive enthusiasts, and professional technicians. In addition to providing valuable diagnostic information, these devices are also simple and straightforward to use, making them an essential tool for anyone looking to keep their engine in top condition.

Credit: www.mixinglessons.com
Types Of Compression Meters
Compression meters are used in a variety of industries to measure the pressure of gases, liquids, and other fluids. Depending on your application, there are several types of compression meters available. In this article, we will discuss four types of compression meters: Mechanical Compression Meters, Electronic Compression Meters, Digital Compression Meters, and Ultrasonic Compression Meters.
Mechanical Compression Meters
Mechanical compression meters are an old-school method of measuring compression. They use an analog gauge and a needle to indicate the compression levels by the gas pressure. Although the display is not very accurate, it is still a preferred method by many mechanics and auto enthusiasts. Mechanical compression meters are simple to use and do not require any power supplies. They are also relatively inexpensive and can be purchased at an auto parts store or online.
Electronic Compression Meters
Electronic compression meters are more advanced than mechanical compression meters. They use an electronic sensor to measure the compression levels and display the readings on a digital screen. The digital screen makes it easier to read and provides accurate readings. Electronic compression meters also have additional functionalities such as data logging, temperature compensation, and automatic calibration.
Digital Compression Meters
Digital compression meters are similar to electronic compression meters in that they use a digital screen to display compression readings. However, these meters have a more precise measuring system and offer better accuracy. They can provide more features such as recording multiple measurements, calculating average readings over time, and displaying steady-state data. Digital compression meters are excellent for industrial applications or scientific research work and tend to be more expensive than the other types of compression meters.
Ultrasonic Compression Meters
Ultrasonic compression meters are the latest innovation in compression meter technology. These meters use sound waves to measure the level of compression, making them non-invasive. They work particularly well for gas compressors and offer a more precise measurement of gas flow. Ultrasonic compression meters are complicated and expensive machines that are usually found in industrial processing plants or research laboratories.
Meter Type | Accuracy | Functionality |
---|---|---|
Mechanical | Low accuracy | Simple to use, low cost |
Electronic | High accuracy | Advanced features like data logging, temperature compensation |
Digital | Very high accuracy | Offers additional features like multiple measurements and steady-state data display |
Ultrasonic | High accuracy | Non-invasive, excellent for gas compressors |
Regardless of the type of compression meter required, it is vital to choose a device that meets the user’s needs, accuracy, and budget.
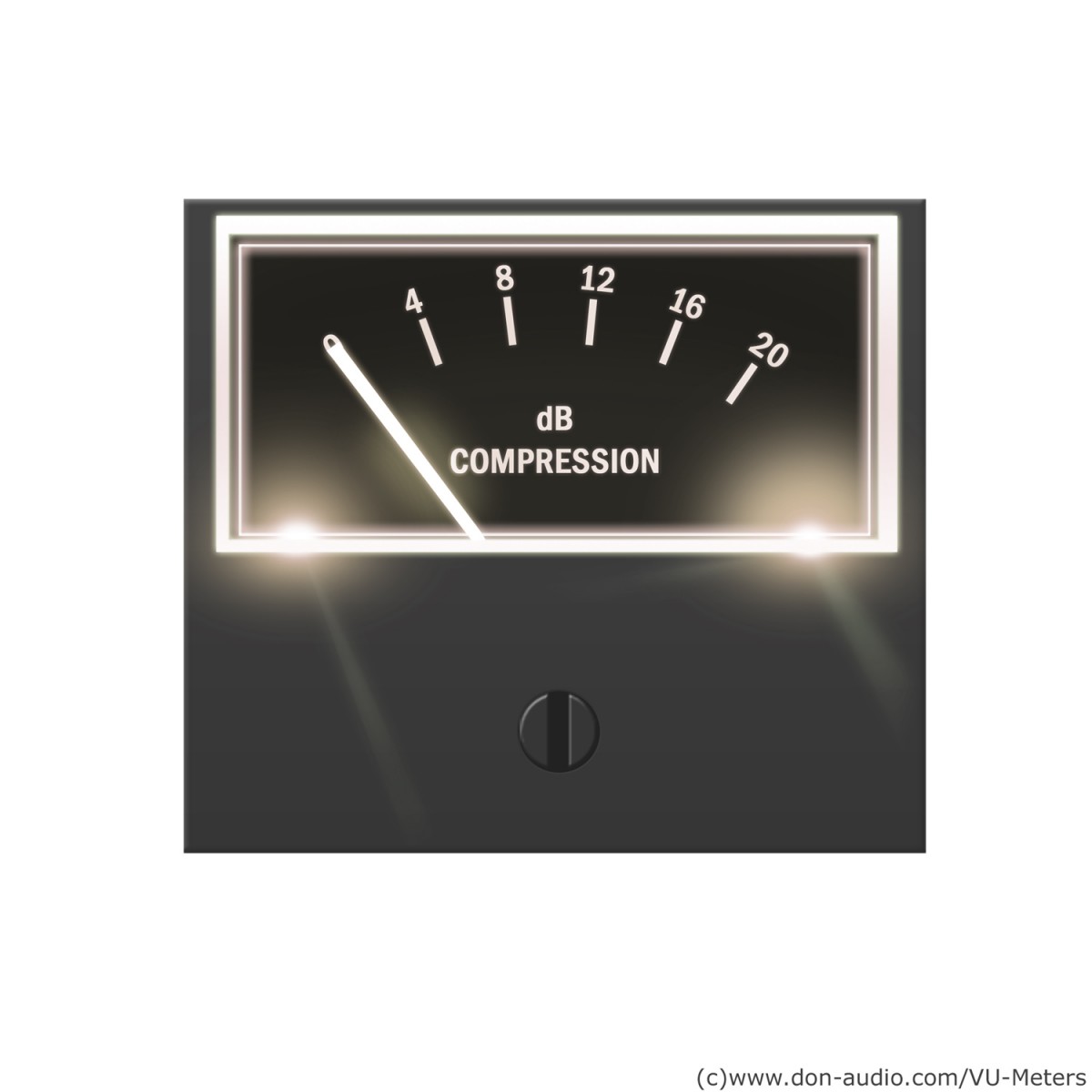
Credit: www.don-audio.com
Applications Of Compression Meters
Compression meters are used to measure and evaluate the pressure within an engine’s cylinders. These tools are widely used within the automotive industry to assess the performance and efficiency of engines. Compression meters can also be used in industrial settings to monitor pressure in machinery.
Whether it is the automotive industry or the petroleum industry, compression meters have diverse applications in several industries. With the help of these devices, companies can closely monitor their industrial processes, ensure precision measurements, and prevent any potential shutdowns. In this article, we will discuss some of the most common applications of compression meters, and how they contribute to streamlining the industrial processes.
Industrial Processes
Compression meters play a crucial role in the industrial sector as they are an essential tool to monitor and maintain the health of heavy equipment and machines. These meters help detect inefficiencies in the system, allowing for the timely assessment of the machine’s overall performance. In addition, these devices facilitate real-time decision making for factory operators and industrial engineers, minimizing the possibility of shutdowns and expensive repairs.
Automotive Industry
Compression meters have several applications in the automotive industry, ranging from testing engine compression to exhaust gas analysis. These devices help automotive technicians check engine quality, reveal leaks, and perform preventative maintenance. Compression meters also help in troubleshooting potential engine failures, reducing the need for time-consuming diagnoses.
Petroleum Industry
The petroleum industry is perhaps one of the largest beneficiaries of compression meters. The devices help in monitoring the compressor units’ health, which is essential for regulating the flow of gas through pipelines. These meters help regulate the pumping conditions, including temperature and pressure, to maintain the pipeline’s integrity, ensuring that it delivers oil and gas safely.
Power Generation Industry
With growing energy demand, the power generation industry is heavily reliant on precision equipment to ensure the smooth functioning of power plants. Compressors play a critical role in maintaining and regulating the energy supply. Compression meters help plant operators monitor the performance of these compressors, detect any equipment failure, and schedule maintenance to prevent prolonged repair and discharge cycles. In conclusion, compression meters are widely used in various industries for their numerous applications, including monitoring and maintaining the health of equipment and machines. Industries like automotive, petroleum, and power generation, to name a few, rely heavily on the precision of compression meters, ensuring the smooth functioning of processes and preventing shutdowns and expensive repairs.

Credit: www.mixinglessons.com
Frequently Asked Questions For Compression Meters
How Do You Measure Compression Force?
Compression force can be measured using a compression testing machine that applies force and records the results. The machine typically uses a load cell and specialized software to provide accurate readings. The force is applied slowly and steadily until the material being tested is crushed or deformed.
What Is Output In Compression?
In compression, output refers to the compressed version of a file or data. Once compressed, the output file is reduced in size, making it easier to transfer, store or share. The output file should be smaller than the original file but still contain the same information.
What Is A Gain Reduction Meter?
A gain reduction meter is a tool used in audio production to measure how much a compressor or limiter is reducing the amplitude of an audio signal. It is essential in determining the dynamics of a sound and ensuring that the output remains within a specific range.
What Is Compression In Sound?
Compression in sound is the process of reducing the dynamic range of an audio signal. It decreases the volume of loud sounds and amplifies soft sounds to create a more balanced sound. This technique is commonly used in music production, broadcasting and in live music performances to improve clarity and loudness.
Conclusion
The use of compression meters has become increasingly popular in recent years, serving a vital role in the efficient and effective operation of various industries. By measuring the pressure and flow of gas or liquid in a system, compression meters provide essential data for optimal performance and safety.
Proper maintenance and calibration of these devices are crucial to ensuring accurate readings and maximizing their longevity. With advancements in technology, new features and capabilities continue to emerge, allowing compression meters to remain a valued asset in the ever-evolving landscape of industrial operations.