Parallel kick compression is a technique used in audio production to help instruments cut through the mix and create a fuller sound. This technique involves duplicating a track or instrument and compressing it with the same settings as the original, then panning the duplicate track to the opposite side of the stereo field.
This creates the effect of the instrument being present in both ears and helps it stand out in the mix. Parallel kick compression is commonly used on drums, but can also be applied to other instruments such as bass and guitars.
It’s a popular technique among producers and engineers looking to achieve a polished and professional sound.
What Is Parallel Kick Compression
Parallel Kick Compression is a technique used in music production for bringing out the transients or the attack of a sound. It is a technique that has been used by professional sound engineers for years, but with the advent of computer-based recording software, it is now easily accessible to everyone. So, what exactly is Parallel Kick Compression? Let’s explore.
Definition Of Parallel Kick Compression
Parallel Kick Compression is a technique that involves blending a heavily compressed version of a kick drum with the original uncompressed kick drum signal. It is used to bring out the punch or attack of a kick drum.
How Parallel Kick Compression Works
- First, duplicate the original kick drum track
- On the duplicated kick track, add a compressor with a high ratio and a fast attack time
- Set the threshold low enough so that the compressor activates on every kick hit
- Adjust the attack and release times to taste, keeping in mind that a faster attack time will bring out more of the punch in the sound
- Mix the heavily compressed kick drum track with the original kick drum track to taste
- Make sure the compressed kick drum track is not too loud in the mix, as it can quickly become overpowering
Parallel Kick Compression is a powerful tool for enhancing the attack and punch of a kick drum without sacrificing the body of the sound. It is a technique that can be used in any genre of music and is particularly effective in genres like electronic music, hip-hop, and rock.
Now that you understand what Parallel Kick Compression is and how it works, try experimenting with it in your own music productions. Remember, like all production techniques, the key is to use it in moderation and to trust your ears when it comes to mixing.
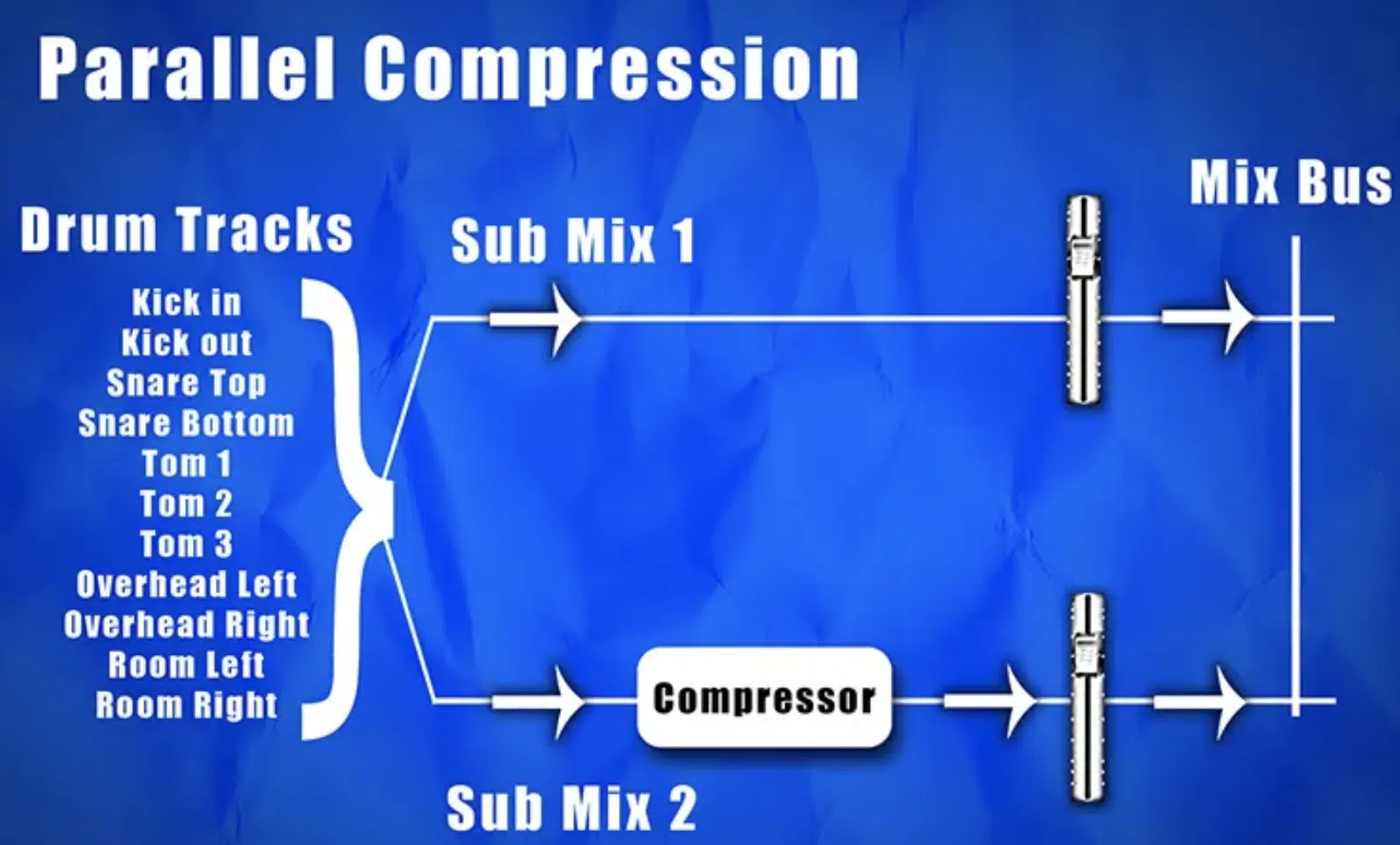
Credit: unison.audio
Applications Of Parallel Kick Compression
Parallel Kick Compression is a highly effective and widely used method of compression, which is why it has numerous applications across various industries. Some of the most prominent applications of Parallel Kick Compression are the following:
Oil And Gas Industry
Besides discovering and extracting oil and gas deposits, the oil and gas industry also often requires extra assistance in transporting and refining these materials for commercial purposes. Strong compression is required to achieve this, which is where Parallel Kick Compression comes in. It makes it possible to maintain multiple stages of compression so that the extracted oil and gas can be efficiently transported and refined.
Industrial Air Compression
Parallel Kick Compression is also used for industrial air compression purposes. In this case, the compressor has multiple stages and is designed to deliver high volumes of air efficiently, and with minimal energy consumption. This makes the Parallel Kick Compression method ideal for a range of industrial applications such as manufacturing, medical, and gas generation processes.
Other Applications
Other than oil and gas extraction and industrial air compression, there are many other applications of Parallel Kick Compression. For example, it is used in the production of polyethylene and other plastics, the vapor recovery process, and chemical manufacturing.
Industry | Application |
---|---|
Oil and Gas | Efficient transportation and refinement of extracted resources |
Industrial | Air compression for manufacturing, medical, and gas generation |
Other | Polyethylene and plastics production, vapor recovery process, chemical manufacturing |
In conclusion, with its multiple stages, ease of use, and energy efficiency, Parallel Kick Compression is a popular compression method that offers numerous applications across a wide range of industries.
Advantages Of Parallel Kick Compression
Parallel kick compression offers numerous benefits for gas processing facilities, including a higher capacity for gas processing, lower energy consumption, and a smaller environmental footprint. With this technology, multiple stages of compression can be combined and operated in parallel, resulting in a more efficient and cost-effective process.
Parallel Kick Compression (PKC) is a technology that has been developed to increase the efficiency and reliability of gas compression systems. PKC is an innovative approach that uses multiple small cylinders in a parallel configuration instead of the traditional large cylinder, allowing for a higher compression ratio and greater system efficiency. In this blog post, we will discuss the advantages of PKC, including efficiency, reliability, and cost savings.
Efficiency
The parallel configuration of PKC cylinders means that each cylinder handles a smaller volume of gas, allowing the system to operate more efficiently. The smaller cylinders generate less friction and heat, improving the overall compression efficiency. Additionally, PKC allows for a higher compression ratio, resulting in a greater amount of compressed gas for each unit of energy used. This increased efficiency leads to lower operating costs and reduced greenhouse gas emissions.
Reliability
PKC systems are designed to be more reliable than traditional compression systems. The use of multiple small cylinders means that if one cylinder fails, the system will still be operational. This redundancy reduces downtime and maintenance costs. Additionally, PKC systems are designed to operate at a lower RPM, resulting in less wear and tear on the components and increased system lifespan.
Cost Savings
Finally, PKC provides significant cost savings over traditional compression systems. The increased efficiency and reliability of PKC systems reduce operating and maintenance costs. The lower RPM operation also reduces maintenance and replacement costs. Additionally, the smaller footprint of PKC systems means that they require less space for installation, resulting in reduced construction costs. In conclusion, the advantages of PKC systems are significant and make it an attractive option for gas compression applications. The increased efficiency, reliability, and cost savings make PKC ideal for use in a variety of industries.

Credit: www.youtube.com
Components Of Parallel Kick Compressor
Parallel kick compressors have several components, including two or more compressor cylinders, intercoolers to cool the compressed air, and an aftercooler to reduce the air temperature further. These components work together to efficiently compress air, making them ideal for several applications, including natural gas processing and transportation.
Components of Parallel Kick Compressor Parallel kick compressors are high-performance compressors used for heavy-duty industrial applications such as oil and gas processing and petrochemical plants. A parallel kick compressor is an effective compressor that consists of multiple cylinders, pistons, valves, intercoolers, and aftercoolers. These components work in tandem to deliver high compression ratios and increased efficiency. H3: Cylinders Cylinders are the heart of a parallel kick compressor. They create the compression of the gas and allow it to be transferred between stages. It is a closed metal structure that enables the piston to move in a linear motion. Each cylinder contains a piston, a valve, and some other components that work together to compress the gas. Typically, a parallel kick compressor has multiple cylinders to provide better compression. H3: Pistons Pistons are the moving components inside every cylinder of the parallel kick compressor. They move in a linear motion, compressing the gas inside the cylinder. The pistons are responsible for transferring the compressed gas from one cylinder to another. Typically, parallel kick compressors have two or more pistons inside each cylinder, which move back and forth with the help of a crankshaft. H3: Valves Valves are crucial for maintaining the air flow inside the parallel kick compressor. They regulate the gas pressure and control the flow of the gas while it moves between stages. At every stage, there are two valves, one for suction and one for discharge. The suction valve allows the gas to enter into the cylinder, and the discharge valve releases the compressed gas. The valves in a parallel kick compressor are designed to work together, ensuring maximum efficiency. H3: Intercoolers Intercoolers are essential for the efficient operation of the parallel kick compressor. They are located between the cylinders and cool the gas by removing the heat generated during compression. They help the compressor to reject heat from the system and prevent any damage to the downstream equipment. The intercoolers also reduce the workload on the compressors, which helps to increase the compressor’s lifespan. H3: Aftercoolers Aftercoolers help in the final stage of parallel kick compressor operation. They are used to cool the compressed gas after it leaves the compressor. This cooling process further reduces the temperature of the gas and increases its density. Lowering the temperature and increasing the gas density before sending it to downstream equipment increases the compressor’s efficiency. The aftercoolers also remove any remaining moisture in the compressed gas, preventing damage to equipment and increasing the system’s life span. Overall, the components of a parallel kick compressor must be maintained and optimized to ensure long life, maximum efficiency, and safe operation. The use of quality parts and regular maintenance is crucial in ensuring optimal performance and a long service life for the compressor.
Maintenance Of Parallel Kick Compressors
Proper maintenance is crucial for the uninterrupted performance of parallel kick compressors. The compressors need regular check-ups, timely replacement of parts, and lubrication to remain operational and avoid any downtime and production loss.
Maintaining parallel kick compressors is vital for their efficient functioning and maximizing their lifespan. Regular inspections, proper lubrication, and cleaning are key components of maintenance, as well as monitoring for potential issues through troubleshooting.
Regular Inspections
Regular inspections play an important role in detecting any potential issues before they become significant problems. Inspections should include checking the alignment of the parallel kick compressors, ensuring that all the components are properly secured, and verifying that there are no leaks or corrosion. In addition, it is important to keep a record of any issues found during inspections to track patterns and anticipate future problems.
Proper Lubrication
Proper lubrication of parallel kick compressors is crucial to ensure their smooth functioning. Lubrication helps to reduce friction and wear of the moving parts, thus helping to extend the life of the compressor. The amount of lubrication needed will depend on the type of compressor and the environment it is operating in. It is essential to use the correct type of lubricant and to follow the manufacturer’s instructions for application and frequency of application.
Cleaning
Cleaning is essential for the smooth operation of parallel kick compressors. The accumulation of dirt and debris can cause clogs, overheating, and damage to the compressor. Cleaning should be done on a regular basis, depending on the operating environment and the manufacturer’s recommendations. This includes cleaning the exterior, the air intake, and the internal components. It is important to use appropriate cleaning materials and to avoid damaging any delicate components.
Troubleshooting
Despite regular inspections and maintenance, issues may still arise with parallel kick compressors. Troubleshooting involves identifying the problem and taking appropriate action to resolve it. This may involve checking for loose components, leaks, or damage, and repairing or replacing any faulty parts. In addition, troubleshooting may involve adjusting settings, such as pressure or temperature, to optimize the compressor’s performance. In conclusion, regular inspections, proper lubrication, cleaning, and troubleshooting are essential for maintaining parallel kick compressors. By following these maintenance practices, you can ensure that your compressor runs efficiently and prolong its lifespan.
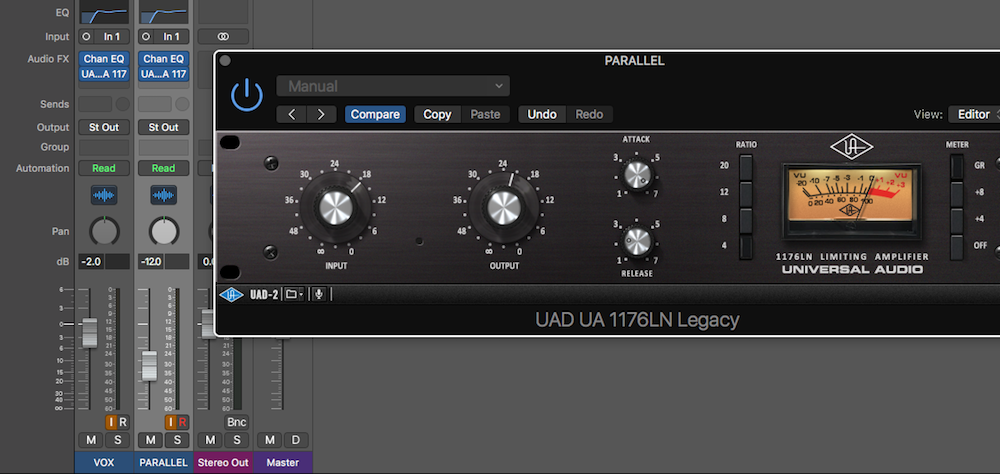
Credit: producelikeapro.com
Comparison With Conventional Compression
Parallel kick compression offers clear advantages over traditional compression methods, such as higher efficiency and faster processing speeds. In comparison to conventional compression, it reduces the processing time and minimizes energy consumption while improving performance, making it a superior choice for companies seeking a more efficient compression solution.
Parallel kick compression is a technology that has significantly improved the performance of air compressors. When it comes to conventional compression, the design, and performance of these compressors differ considerably. In this section, you’ll explore the differences in design and performance comparison between parallel kick compression and conventional compression.
Differences In Design
The design of parallel kick compression differs from that of conventional compression in several ways. Firstly, parallel kick compression utilizes a parallel configuration of multiple compressor stages to increase efficiency. In contrast, conventional compression systems rely on single-stage compressors that operate at a higher pressure ratio, leading to greater energy consumption. Additionally, parallel kick compressors feature an inter-stage coolers and heat exchangers, allowing for better thermal management and increased reliability. In contrast, conventional compressors lack these features, leading to a greater risk of overheating and breakdowns.
Performance Comparison
Compared to conventional compressors, parallel kick compressors offer a range of performance benefits. For instance, parallel kick compression is capable of processing larger volumes of gas with higher discharge pressures, making it ideal for heavy-duty applications. In contrast, conventional compressors are limited in the volume of gas they can process. Moreover, parallel kick compressors are more energy efficient, with a lower specific power consumption compared to conventional compressors. This means higher energy savings and reduced operating costs over the long term. Overall, parallel kick compression is a superior technology that offers improved performance and energy efficiency compared to conventional compression systems. With its unique design and performance capabilities, it’s no surprise that parallel kick compression is increasingly becoming the preferred technology for heavy-duty industrial applications.
Future Of Parallel Kick Compression
Parallel Kick Compression has the potential to revolutionize data storage and access by enabling faster data transfer rates and reducing latency. With advancements in technology, the future of Parallel Kick Compression looks bright, offering improved performance and efficiency for various applications and industries.
Parallel kick compression is a technique that has been around for some time now, but the future of this technology is looking brighter than ever. With continued advancements in technology and the potential for growth in various industries, parallel kick compression may become the go-to choice for enhancing performance and efficiency. In this post, we will explore some of the aspects of the future of parallel kick compression, including advancements in technology and potential areas of growth.
Advancements In Technology
Advancements in technology have played a significant role in the development of parallel kick compression. In recent years, we have seen an increase in the use of machine learning and artificial intelligence, which has led to the creation of more powerful and efficient compressor systems. These systems can analyze data and make real-time adjustments to optimize performance, resulting in higher levels of efficiency and energy savings. Additionally, the development of more sophisticated algorithms and software has also led to the creation of more customizable compressor systems. With the ability to customize compression settings based on specific industry requirements, businesses can optimize their operations and save on operating costs.
Potential Areas Of Growth
There are many potential areas of growth for parallel kick compression in various industries. For example, in the energy industry, parallel kick compression has the potential to improve the efficiency of gas turbines, resulting in reduced emissions and increased energy production. In the manufacturing industry, parallel kick compression can be used to improve the efficiency of pneumatic systems, resulting in increased productivity and reduced operating costs. Similarly, in the automotive industry, parallel kick compression can be used to improve the energy efficiency of combustion engines, resulting in reduced fuel consumption and lower emissions. In conclusion, the future of parallel kick compression is bright, with continued advancements in technology and potential areas of growth in various industries. As more businesses realize the benefits of parallel kick compression, we can expect to see widespread adoption of this technology in the coming years.
Frequently Asked Questions For Parallel Kick Compression
What Should Parallel Compression Settings Be On Kick Drum?
For parallel compression on kick drum, start with a low compression ratio around 2:1 or 3:1, and a moderate attack time between 10-30ms. Set the release time to match the tempo of the track. Adjust the threshold to achieve a gain reduction of 3-6dB.
Finally, blend the compressed signal with the dry signal to taste.
What Is The Point Of A Parallel Compression?
Parallel compression is a mixing technique that is used to add more depth, power, and control to audio. This technique involves duplicating the original audio signal, compressing the duplicate, and then blending it back with the original signal at a lower volume.
The result is a more even sound with improved dynamic range and sustain, without losing the natural sound and character of the original signal.
What Is The Best Compression Setting For Kick?
The best compression setting for kick depends on the track itself, mixing style, and the sound you’re going for. A good start is a ratio of 4:1 with an attack of around 10ms and a release of around 100ms. However, it’s important to experiment and adjust the settings to achieve the desired sound.
How Much Compression Should A Kick Drum Have?
The amount of compression required for a kick drum depends on the desired sound. Generally, a ratio of 4:1 or higher is used to control peaks and even out the sound. The attack and release times should be set to match the drum’s natural decay.
It’s important to experiment with the settings to achieve the desired result.
Conclusion
To sum up, parallel kick compression is a technique that can greatly improve the quality of your audio recordings. By using this method, you can enhance the impact of your kicks and produce a more dynamic mix. It’s a simple yet effective tool that can help take your music to the next level.
Whether you’re a professional sound engineer or a budding music producer, parallel kick compression is definitely worth considering as part of your toolkit. So, try it out and see the difference for yourself!